Overlooking the upper floor of the new 350 ton HPP.
Grøntvedt Nutri in Norway has started operating the largest HPP Protein Plant built to date. The plant has a daily capacity of 350 tons of raw material, predominantly herring and mackerel offal from Grøntvedt‘s pelagic operations in the town of Uthaug at the mouth of Trondheim fjord.
Grøntvedt Pelagic is the world‘s largest producer of marinated herring and mackerel and has a major market share in the Nordic countries. It also produces frozen herring and mackerel.
Grøntvedt Pelagic has traditionally processed and sold offal as silage, for use as fertiliser in agriculture and farming. For greater profitability and sustainability, Grøntvedt ordered the king-size HPP in 2019 for production of fishmeal and fish oil from the thousands of tons of offal generated annually.
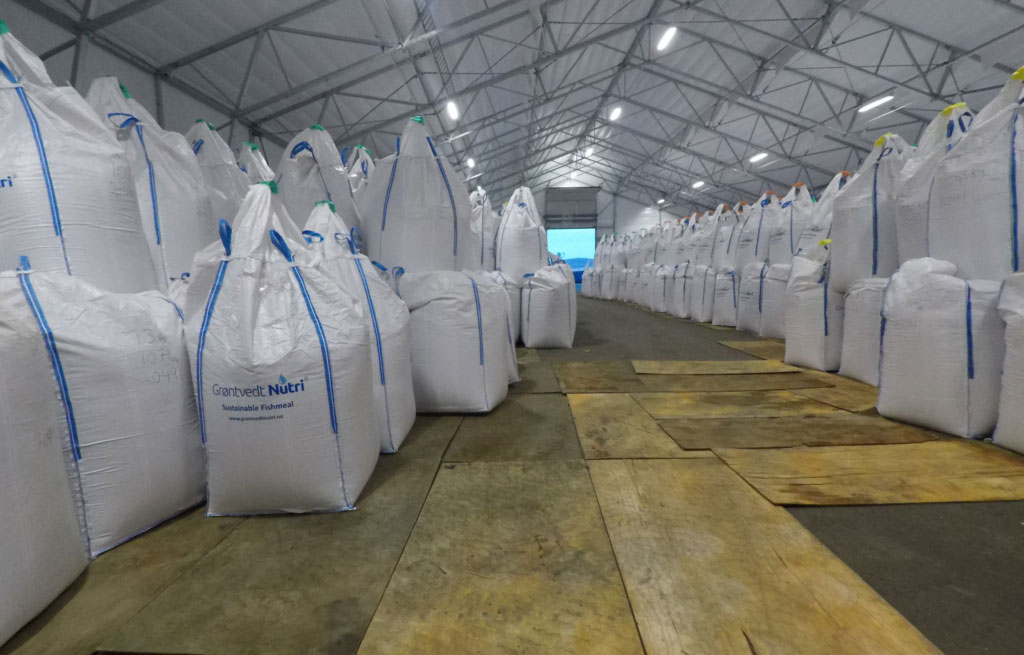
Fishmeal from the Grøntvedt Nutri HPP waiting to be shipped to customers.
Approved for human consumption
Production trials started late in 2020 and maximum efficiency is expected to be reached early in 2021. Fishmeal and fish oil is produced and sold under the Grøntvedt Nutri trademark. Already in 2020, a selection of the products got approved for human consumption by the Norwegian Food Authority (Mattilsynet), according to the Grøntvedt Nutri website.
The HPP process differs from conventional fishmeal and fish oil plants. The HPP has no liquid side, opting instead for two-stage drying. This simplifies the overall process, brings down cost and delivers consistent high-grade products.
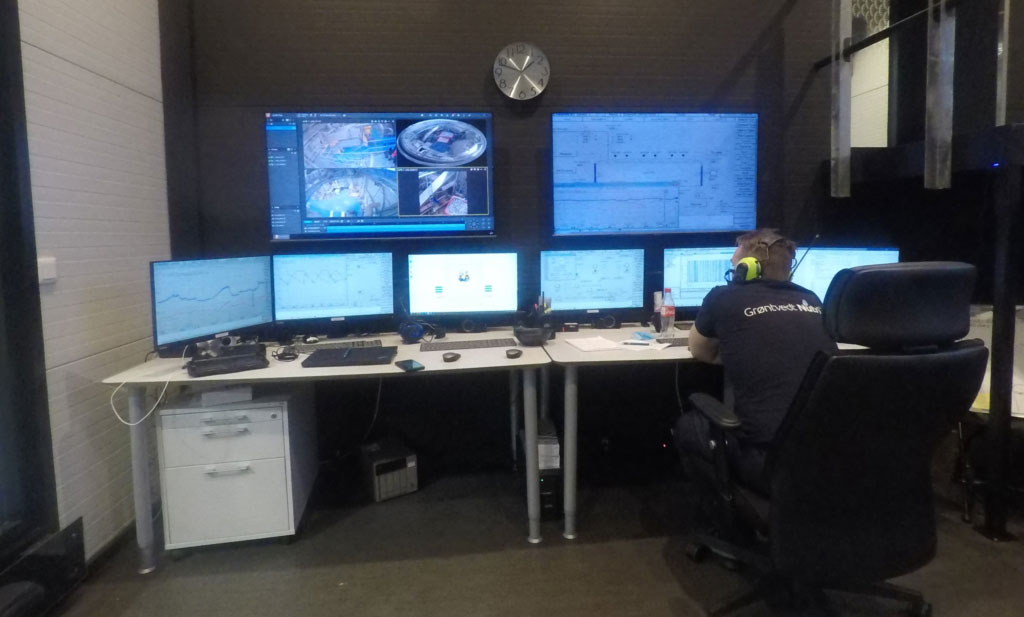
The control centre for the new HPP.
Premium yield
According to Gunnar Pálsson, chief designer of the HPP process, the fresh raw material from Grøntvedt Pelagic has proved to deliver premium products. „The process yields about 15% fish oil and 20% fishmeal from the offal. Herring and mackerel bones have proved to be a very valuable source of protein.“
New facilities in Uthaug
In Uthaug, a new facility was built to house the new two-storey protein plant. A conveyor system feeds the raw material to the plant. After sacking, the fishmeal is moved to a large warehouse for shipping.
On its website, Grøntvedt Nutri emphasizes the importance of adding the Hedinn Protein Plant to its operations:
„Our production takes place in our top modern production plant, with a high technical and hygienic standard. All quality procedures are in accordance with HACCP principles.
Our facility is designed for eco-friendly and sustainable production and has been subjected to an extensive and strict program of approval. The raw material used is exclusively from responsibly managed fisheries approved by the authorities.“
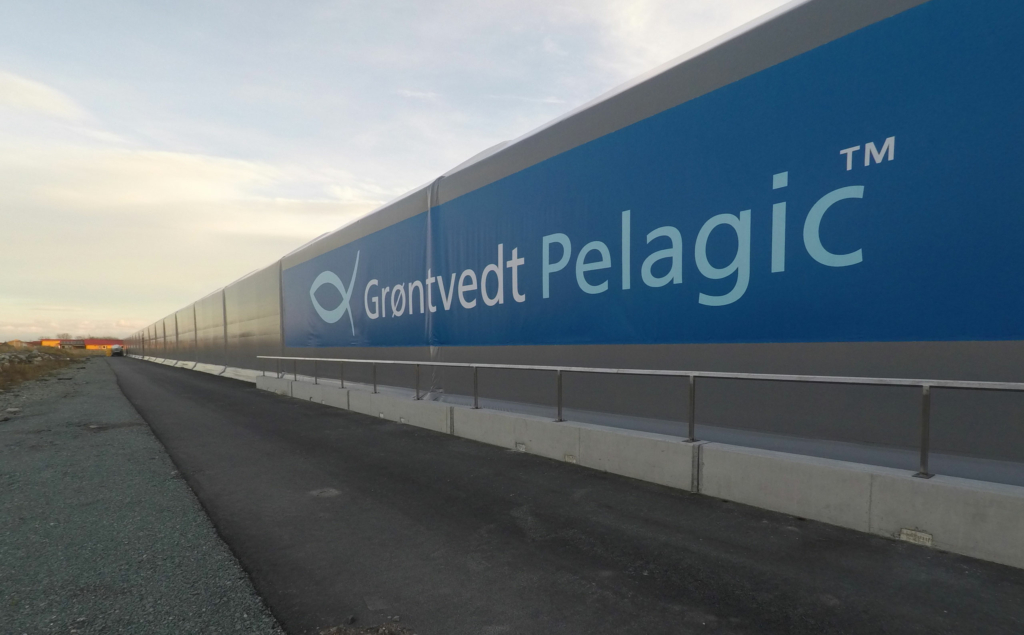
Grøntvedt set up a new warehouse for the temporary storage of products derived from the Hedinn Protein Plant.
The HPP process
The HPP was developed by Hedinn to enable fishmeal and fish oil production at sea and on land in a more economical way than earlier processes would allow. The plant runs on electricity and steam, providing for clean and efficient operation with a high degree of adjustability.
The innovative plant design simplifies the production process, while at the same time improving quality, by reducing the number of main components, process tanks and control parameters. This significantly reduces operating costs, energy use, manpower needs, floor space requirements and use of cooling water.
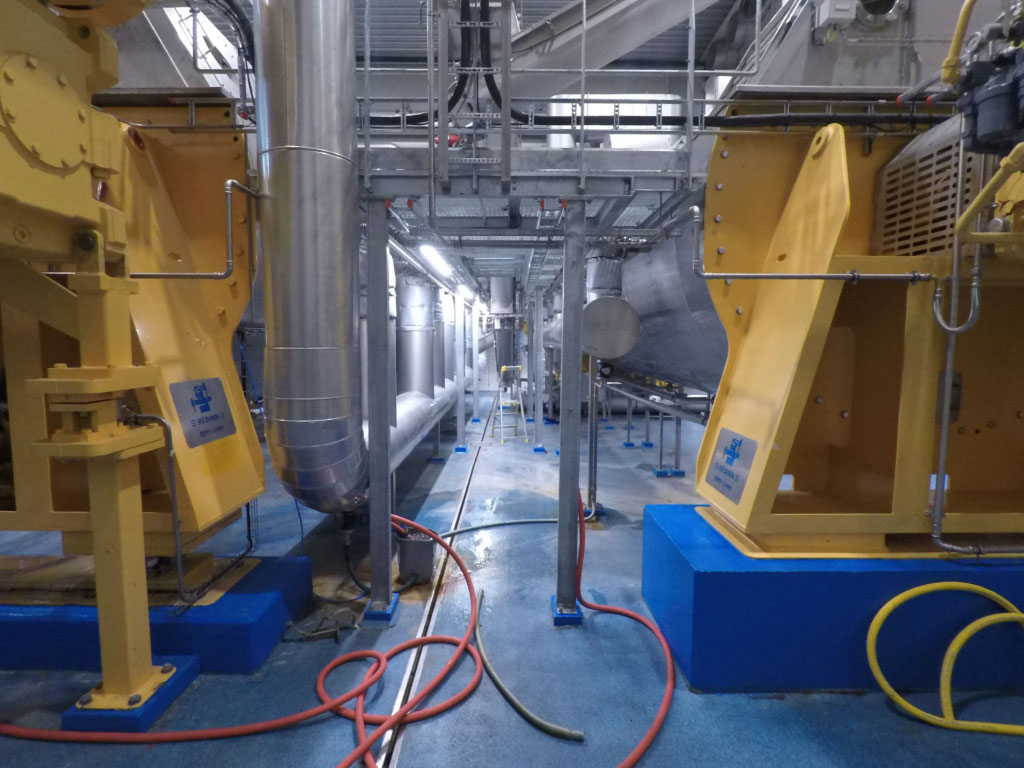
The lower floor of the new protein plant.