Construction of the HPP in Hedinn’s stainless steel department.
The largest Hedinn Protein Plant (HPP) to date is under construction at Hedinn‘s headquarters in Hafnarfjördur, Iceland. The plant will have a daily capacity of 350 tons of raw material. The largest HPP built before this one can process 125 tons of raw material daily.
This latest HPP is being constructed for Grøntvedt Pelagic in Uthaug at the mouth of Trondheim fjord, Norway. The Grøntvedt family herring business has been around for almost two centuries. It is now run by the 8th generation of Grøntvedts. The company is the worlds largest producer of marinated herring and has a major market share in Scandinavia. It also produces frozen herring and mackerel. Grøntvedt Pelagic has a staff of 120-140.
The largest Hedinn Protein Plant (HPP) to date is under construction at Hedinn‘s headquarters in Hafnarfjördur, Iceland. The plant will have a daily capacity of 350 tons of raw material. The largest HPP built before this one can process 125 tons of raw material daily.
This latest HPP is being constructed for Grøntvedt Pelagic in Uthaug at the mouth of Trondheim fjord, Norway. The Grøntvedt family herring business has been around for almost two centuries. It is now run by the 8th generation of Grøntvedts. The company is the worlds largest producer of marinated herring and has a major market share in Scandinavia. It also produces frozen herring and mackerel. Grøntvedt Pelagic has a staff of 120-140.
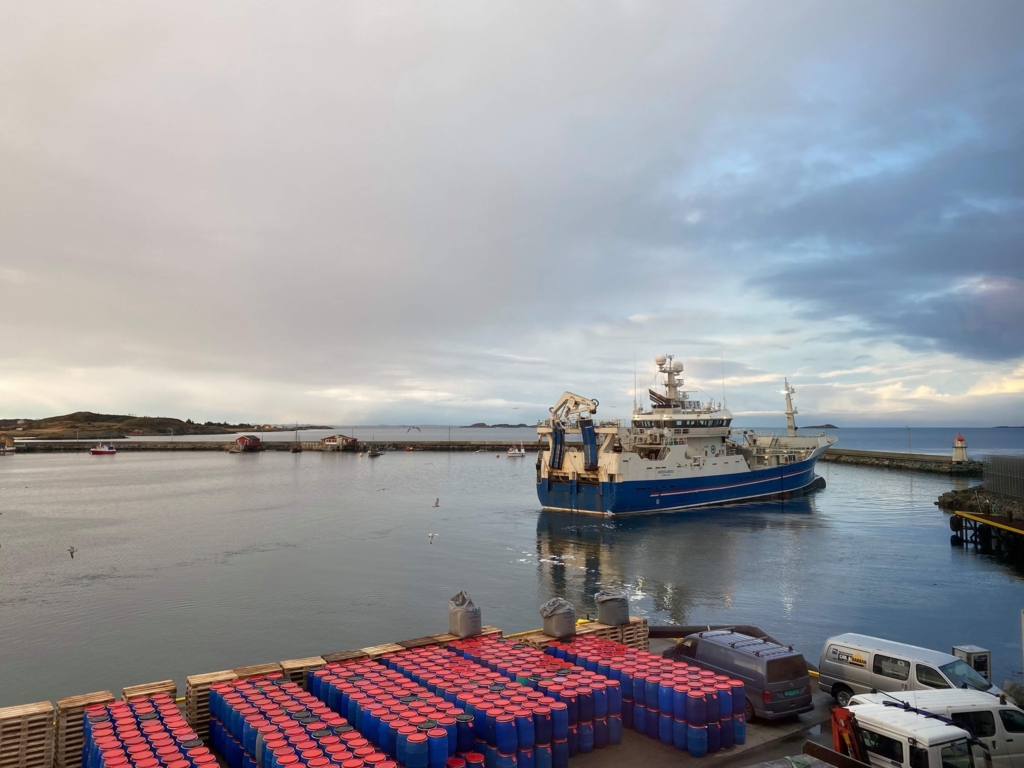
Gröntvedt Pelagic AS operates in Uthaug/Brekstad in Norway.
Grøntvedt has traditionally processed and sold offal as digestate, for use in agriculture and farming. The company went into talks with Hedinn early in 2019, coming to the conclusion that it was viable to commission an HPP to produce fishmeal and fish oil from the large quantities of offal from the herring process, which amount to thousands of tons a year. Hedinn‘s technical department started designing the plant in the summer, scaling up almost every component of the plant due to its large size. But even if the HPP for Grøntvedt has a 50 times greater capacity than the smallest HPP made, the layout and production process is the same. The HPP design simplifies fishmeal and fish oil production, while at the same time improving quality, by reducing the number of main components, process tanks and control parameters in comparison with conventional processing plants. This significantly reduces operating costs, energy use, workforce needs, floor space requirements and use of cooling water.
The components for Grøntvedts protein plant are pre-fabricated in Iceland, Romania, Germany and England. Setup and testing are expected to take several weeks, and production start is planned in late summer of 2020.
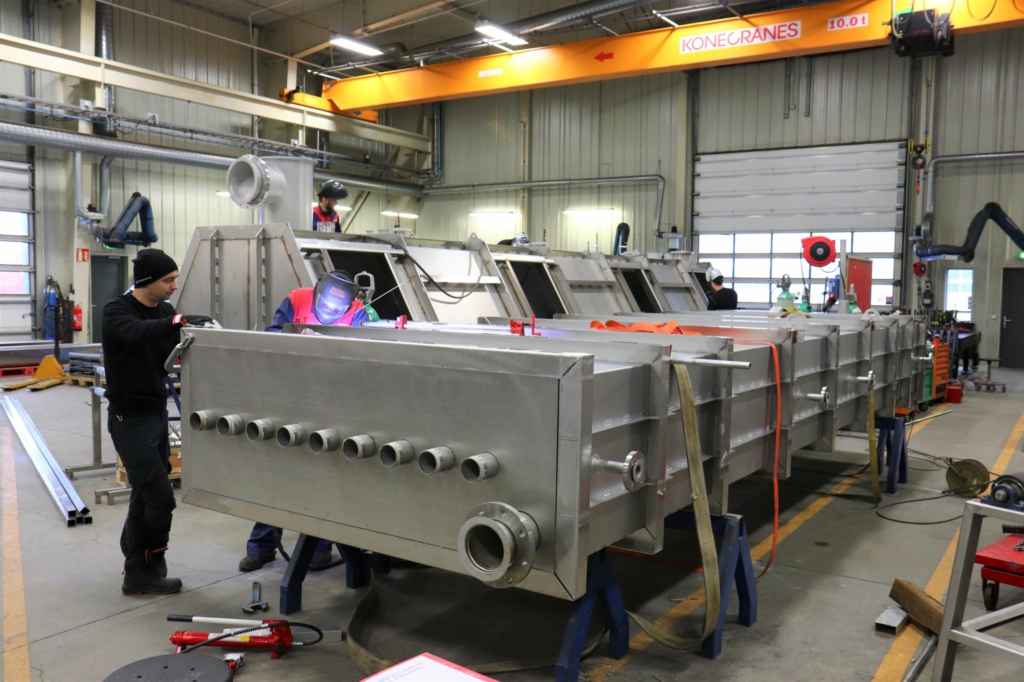
Working on a component in the new HPP for Gröntvedt.